Lithrone GX40RP advance for Further Productivity and Quality Improvement: 24-Hour Central Tokyo Integrated Production Facility Specializing in Short Lead Time Small-lot Production
Japan, Vanfu Co., Ltd. | Lithrone GX40RP advance [GLX-840RP-A]
24 January 2024
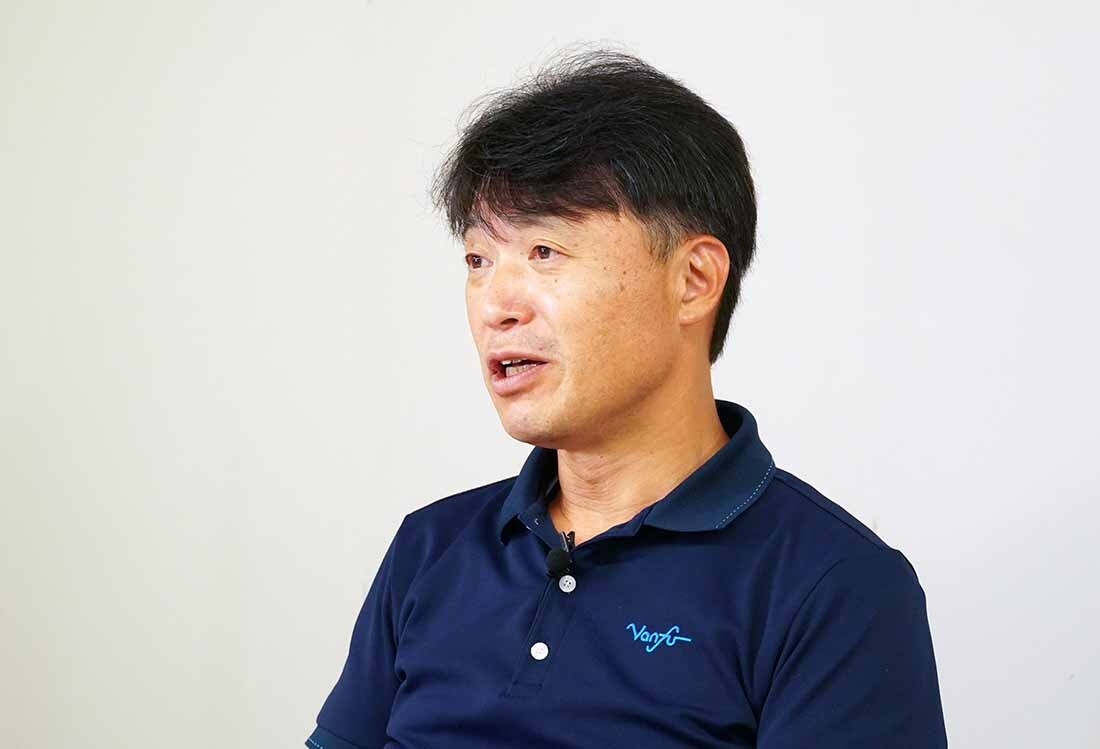
Vanfu Co., Ltd. operates a 24-hour printing facility (Takebashi Printing Center) in the heart of Tokyo, providing a one-stop production system from order receipt to printing, processing, and shipping. The company's greatest strength, taking advantage of its location, lies in small-lot printing and short lead time production, with the ability to accept and send orders on the same day. To further enhance their services, the company is promoting automation and labor-saving. In January 2023, they introduced the Lithrone GX40RP advance (40-inch dedicated perfecting offset printing press) and began full operation. We spoke to President and Representative Director Takayuki Suto, Vice President Shin Yamano, Production Management Section Manager Nozomu Hikichi, and Printing Section Manager Takuya Matsuda about the background, operational status, and effects of the introduction.
Takayuki Suto, President and Representative Director
Prioritizing customer requests and providing customer-centric services
Vanfu Co., Ltd. was founded in 1980 as a phototypesetting and platemaking company, and with the rise of desktop publishing the company launched a shop-type service bureau specializing in platemaking for professional users. Building on their DTP expertise, Vanfu ventured into the on-press proofing business. Currently they offer a one-stop service from order receipt to printing, processing, and shipping. The company has three sales channels: "Sales," "Shop," and "Internet," allowing users to choose the appropriate channel based on their needs.
President Suto explains, "From the beginning, we have focused on the concept of 'providing the necessary amount at the necessary place when needed,' which aligns with sustainability. 'Small lots' and 'short lead time' have been our concepts. We have business with about 20,000 companies, and over 90% are local customers in Tokyo. Time is a crucial factor for our Tokyo customers, so we have adopted a production system that allows us to deliver the products immediately without assigning presses. All employees are highly motivated and constantly researching how to fulfill customer requests promptly. This is an essential condition for achieving short lead times."
Inside the Takebashi Printing Center, where same-day evening shipping is achieved. The facility is equipped with automated production equipment for transport, packing, and shipping of plates and printed materials. In September of this year, four cutting machines were replaced with the Apressia CT115 (Programmable Hydraulic Clamp Cutter) which commenced operations.
Division of work between people and machines along with active promotion of automation and labor-saving
To handle numerous projects, Vanfu focuses on automation and labor-saving in production. "We are advancing automation from the point where data is received to delivery, and we separate the roles of people and machines. For example, we automatically check the data received from customers. Internet projects are automatically impositioned for gang-run printing, including paper type, delivery time, weight, color, and finishing, thanks to our own unique technology. We strive to provide customers with short lead times and low-cost printing services," says President Suto.
He adds, "'Accepting all requests and not refusing any customer request' is our motto, so we handle a wide range of products."
Effect of Lithrone GX40RP advance introduction
"The Lithrone GX40RP advance achieves precise alignment even with challenging 0.06mm thin paper thanks to stable paper transport in one-pass double-sided printing."
Nozomu Hikichi, Section Manager
Attending a tour of the Tsukuba Plant was the spark that led the company, which previously owned multiple other perfectors, to consider introducing the Lithrone GX40RP advance.
"The precision of the Lithrone GX40RP press's front-back registration was impressive. We conducted a printing test using the press under the same conditions as for difficult jobs at our company. The short makeready time and outstanding printing quality with the press made it very attractive to us. Additionally, during a tour of the manufacturing process, we were impressed and thought, 'This manufacturer is amazing,' and simultaneously we believed that the Komori press could withstand the high usage demands of our workload," he noted.
After the introduction, President Suto expressed his satisfaction: "Choosing the Komori press was the right decision. First, the support was very reassuring. There were unexpected challenges since it was a new press for us, but Komori provided us with solid support until it was fully operational. Furthermore, the introduction of the new press boosted the motivation of the operators. Maintenance became routine, and the conscious effort to use the machine carefully positively influenced quality."
Changes in production through double-sided printing with single-sided gripping and automated devices
Nozomu Hikichi, Section Manager in charge of Production Management, notes, "With the single-sided gripper system and no need for flipping the sheets, productivity has improved significantly. Quality has also seen a remarkable improvement. It is used as a dedicated press for sales projects, and customer evaluations of the quality have risen. During the busy period half a month after the launch of full operation, it delivered higher productivity than any other press."
Addressing the effect of the installation he further states, "The A-APC (Asynchronous Automatic Plate Changer) completes job changeover in about 3 minutes since plate changing and blanket cleaning are performed in parallel. From a quality assurance perspective, the PQA-S (Inline Print Quality Assessment System) has proven invaluable. Inspection levels can be finely adjusted, and marking by automatic number tape insertion is accurate."
Takuya Matsuda, the Printing Section Manager, assessed the press, stating: "The ease of getting the right registration with single-sided gripping and adjustability are significant advantages. With the press of a button, it automatically performs front-back registration, reducing the burden of operations. We use the Komori press for jobs with challenging registration requirements, particularly such as outline or intricate characters. Additionally, the PDC-SX (Spectral Print Density Control) function, which adjusts color while measuring, is more accurate than human correction and has proven to be extremely helpful."
From left: Shin Yamano, Vice President; Nozomu Hikichi, Production Management Section Manager; Takuya Matsuda, Printing Section Manager
"The Lithrone GX40RP advance faithfully reproduces colors, so we use it as a dedicated machine for sales projects."
Shin Yamano, Vice President
"Thanks to the high precision of front-back registration, operators can concentrate on color. The stability of the delivery is also highly beneficial."
Nozomu Hikichi, Production Management Section Manager
"The Komori machine eliminates the need for adding IPA to dampening solution, thus reducing the environmental impact. Moreover, the rubber rollers have a longer service life."
Takuya Matsuda, Printing Section Manager
Creating value at the company factory and optimizing print management
President Suto talked about his vision for the future: "The improvement of press functionality and performance not only enhances product quality but also boosts the morale and confidence of operators and sales personnel. While we currently focus on thin paper, we aim to expand into small-lot package printing. We want to create value that can only be produced in this factory by combining our know-how with new elements. We have begun initiatives related to sustainability, including VOCs and our carbon footprint. Furthermore, we plan to put even more effort into print management, proposing optimal printing solutions for our customers."
"With an awareness that 'anyone can do it,' the operation is currently handled by veterans. However, we aim to assign responsibility to younger staff in the future."
Vice President Shin Yamano