KP-Connect Pro Initiates Printing Digital Transformation with Visualization of Schedule and All Processes
Japan, Ko-seikan Co., Ltd. | KP-Connect Pro
21 June 2023
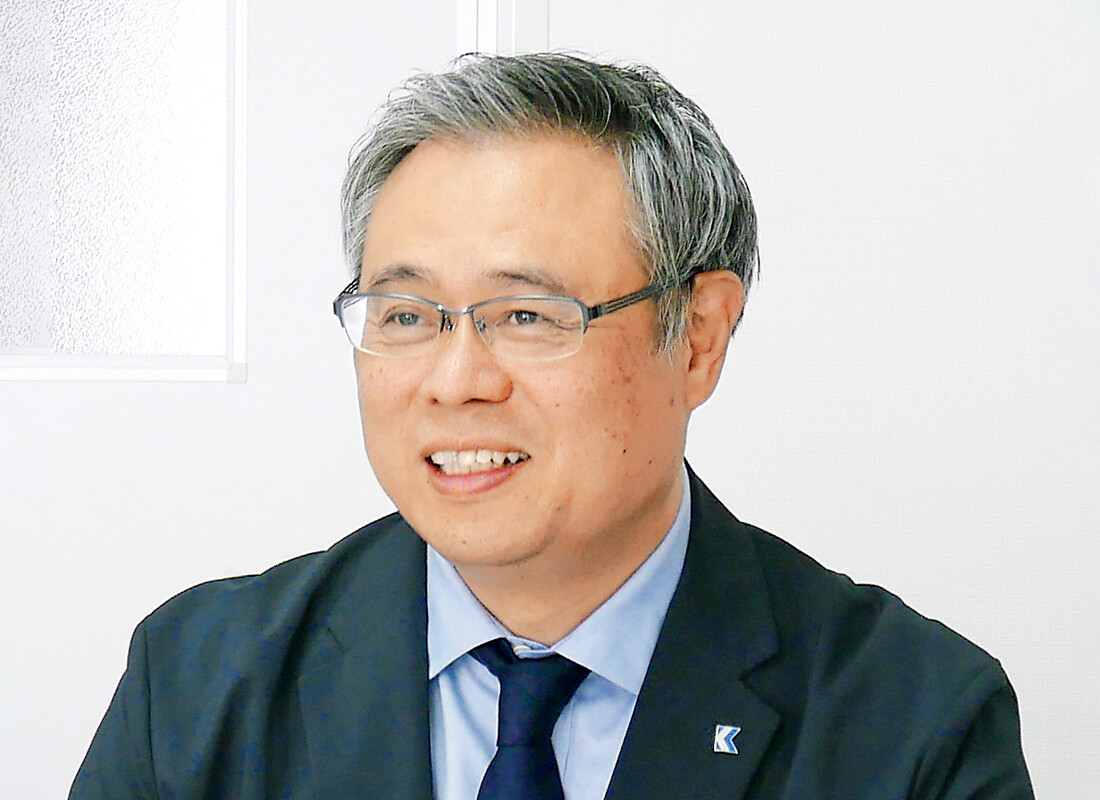
Ko-seikan Co., Ltd. celebrated its 85th anniversary this year. The company formed a business alliance with the Tenmaya department store in 1969 and is currently a wholly-owned group company of Tenmaya. Koseikan's main business is planning, design production, printing, and web production. Beginning in 2021, the company started the digital transformation of printing using KP-Connect Pro and achieved great results in improving production management efficiency and changing the consciousness of employees.
"Thanks to KP-Connect Pro, our company, which had suffered from a technological lag, is now able to proceed with digital transformation." -- Masao Uchida, President and Representative Director
We asked Masao Uchida, President and Representative Director, Kaoru Iwai, Director and General Manager of the Management Department, Kazuhusa Yorizane, General Manager of the Management Team, Koichi Oda, General Manager of the Manufacturing Team, and Ikuko Yanagihara, Manager of the Process Control Group of the Management Team, about Koseikan's digital transformation of printing and its introduction of KP-Connect Pro.
At the manufacturing site, 15 operators are working on multi-skilled printing and processing.
Management and site prior to introduction of KP-Connect Pro
Koseikan previously extracted data from the MIS, edited plans for each production machine on Excel, listed them, and output them on paper. Meetings of representatives of each site were held twice each day, at midday and in the evening. Then responses were provided to progress reports for each item from the person in charge at the site, but there was frequent back and forth about "Which is the latest information?" This sort of confirmation also frequently took place among sales, design, and platemaking staff. Since job priorities often changed, operations that relied on people caused interruptions and waste due to information communication lags (timing delays), significantly reducing process management effectiveness.
In addition, the company's factory has three sheetfed offset presses (one from Komori and two from other manufacturers), one webfed offset press (from Komori), one POD system (from other manufacturer), three cutting machines (from other manufacturer), and one folder (from other manufacturer). Since machines from multiple manufacturers were in operation, centrally managing and visualizing the progress of each machine was thought to be difficult.
Director Iwai said, "When I visited an advanced company that always shared the status of the printing site with the sales department, I realized that our company was lagging behind. However, even though we tried to tackle digital transformation, it was not possible to achieve this," he said. During this time, he encountered KP-Connect Pro. "I was shocked to learn of the existence of KP-Connect Pro as a digital system capable of managing all processes in a printing factory in cooperation with MIS and decided to introduce KP-Connect Pro," he said
Improvement brought by KP-Connect Pro
The daily report is managed on an iPad regardless of the manufacturer. "It's very easy to understand that you can input on the iPad. I think anyone can start using KP-Connect Pro right away since by using an iPad, you can record data from older machines or machines from other companies that cannot directly collect data," said Director Iwai.
The introduction of KP-Connect Pro made it possible to visualize the schedule and progress of all processes, resulting in many improvements.
The first was the reduction of one person in charge of scheduling printing. Since the scheduler automatically calculates each job's load based on standard times, there is no longer a need for dedicated staff working on schedules, and the staffer is now working in another department which needed staff. The second effect is the abolition of process meetings, eliminating the need to prepare meeting materials and reducing the time for responding to inquiries. Since KP-Connect Pro can always check the latest information on the schedule and progress, from handing over press-ready plates to finishing, the number of inquiries about progress has drastically fallen. Two daily process meetings are no longer necessary, and staff can use their time effectively. The third effect is shortening the time for entering on-site daily work reports. Inputting daily reports on the iPad helps to reduce the amount of work that is necessary, including for daily reports on other manufacturers' machines, and makes information real-time.
In addition, the company utilizes such visualized information in a variety of ways. General Manager Yorizane says of its effectiveness: "Being able to see each machine's load status makes it easier to distribute the workload, and we almost never outsource work. If there is no work in the morning due to the previous day's press-ready plate situation, it's now possible to stagger working hours, which can reduce unnecessary overtime work." Process Control Group Manager Yanagihara, who is in charge of process management, says, "Being able to see the progress of each department has changed my awareness of the schedule." The sales/production and manufacturing sites were working at different bases, although there were issues with information sharing. However, since the conditions for receiving final data and the press-ready plates became visible, the consciousness of sales also changed and the delay in receiving final data disappeared.
Cooperation with MIS and improvement due to KP-Connect Pro
Manager Yanagihara operates the KP-Connect Pro scheduler. "Once the initial settings are solid, all you have to do is input the job information and the day's process schedule will be completed. I think dependence on people is being solved."
The operation status of each machine obtained by KP-Connect Pro is also linked to MIS, and cost management is performed using the data.
In the latter half of 2021, the company called on its employees to "become an organization that can talk in numbers," and embarked on business transformation. A task force called "margin improvement" was launched and business improvement was promoted. Director Iwai said, "Each team selects a general manager and one member to work on improving the profit margin across the company. KP-Connect Pro data is used in each department for improving operational mechanisms and the workflow." The scope is wide-ranging, including elimination of waste and bottlenecks, reduction of wasteful overtime by improving productivity, and price negotiations for materials and outsourcing costs.
Employee awareness rises and Koseikan can talk in numbers
Regarding the investment effectiveness of KP-Connect Pro, Director Iwai said, "In addition to the cost reduction effect of indirect work of about 6 million yen or more annually, there are effects such as productivity improvement and reduction of overtime work due to visualization."
Only two years after its introduction, KP-Connect Pro has already become indispensable. "We communicate with prepress and postpress while looking at the data. Everyone thinks for themselves and works on their own work, so they have their own opinions, and the organizational culture is improving," says General Manager Oda.
Finally, President Uchida said, "We want to be a company that can provide customers with the maximum synergy of digital and analog, and that can grow with our feet firmly on the ground."
From left: Kaoru Iwai, Director and General Manager of the Management Department; Kazuhusa Yorizane, General Manager of the Management Team; Koichi Oda, General Manager of the Manufacturing Team; Ikuko Yanagihara, Manager of the Process Control Group of the Management Team
"In the future, we would like to analyze the data obtained by KP-Connect Pro and use it to improve the workplace."
Kaoru Iwai, Director and General Manager of the Management Department
"We use KP-Connect Pro to allocate work to each machine so that work can be completed on time. Overtime hours have been reduced by about 25 percent compared to last year."
Kazuhusa Yorizane, General Manager of the Management Team
"We use icons to indicate job status. Sales and production are also aware of this, and we no longer have to wait for plates."
Koichi Oda, General Manager of the Manufacturing Team
"Sales and production staff now contact us spontaneously. Losses due to delays receiving final data have also disappeared, except in cases of customer circumstances."
Ikuko Yanagihara, Manager of the Process Control Group of the Management Team