System 38S H-UV Web Makes International Splash
Quality × Productivity: H-UV WEB
01 April 2014
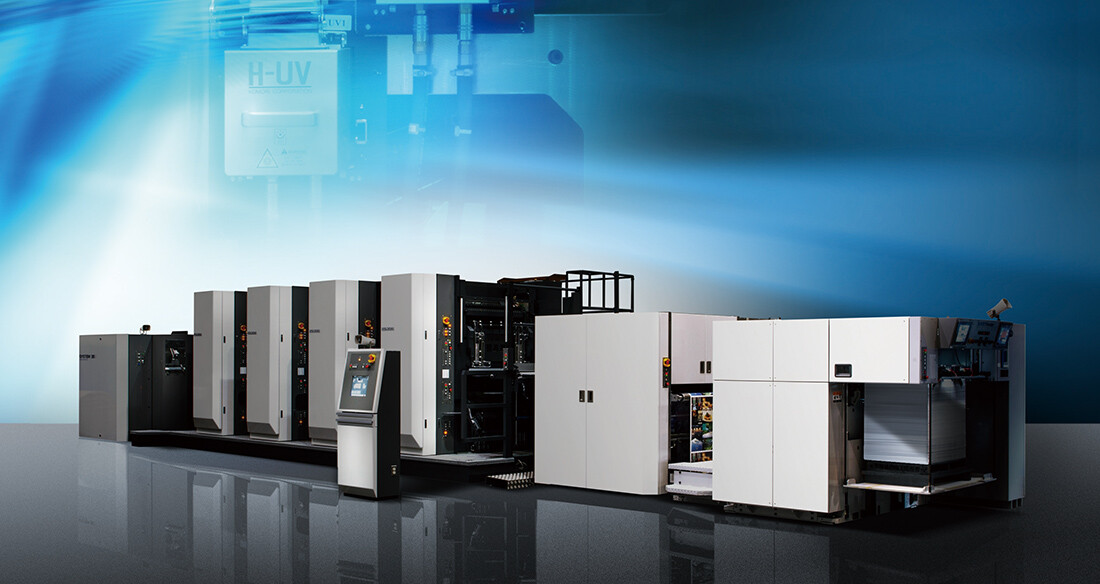
Komori users from all over the globe visited the Tsukuba Plant this spring to witness the international debut of the System 38S H-UV with 625 mm cutoff (LR-438/625S H-UV) web offset press. Also featuring an eight-color Lithrone G40P H-UV, the event delivered a Komori message for printers pursuing a Web-to-print or gang-run printing business model. The two presses ran the same job on the same paper to allow a side-by-side comparison of the H-UV web machine and the high-spec H-UV Lithrone perfector. On Press joined the gathering and spoke to two interested customers.
Innovation the Komori way
The stars were aligned for the integration of Komori's H-UV Innovative Curing System into the company's acclaimed System 35S/38S Series web offset presses. This development means far more than the simple merger of H-UV printing's outstanding performance with the productivity of Komori's 16-page web presses. It is, of course, the graphic impact, the environmental credibility and the operational upsides of H-UV multiplied by the speed, efficiency and raw power of the System machines. But it goes far beyond this. In fact, this transformation enables commercial web presses to go head to head with sheetfed machines and achieve unprecedented success.
Currently in production in Japan, the System machines with H-UV were debuted for international customers this spring at the Tsukuba Plant. Orders are already in double figures -- with many orders coming from sheetfed users.
To a certain degree, Komori's development of this press and the quick acceptance of it by the Japanese industry reflect the growing recognition of the dominance of H-UV technology over other UV systems. Komori has received orders for more than 400 H-UV-equipped sheetfed presses from customers around the globe. Overseas markets are seeing a pickup in the momentum of sales as the competitive advantage of H-UV technology becomes more widely known. Already, shipments of H-UV presses outstrip those of presses with other instant drying systems by a considerable margin.
H-UV web development concept
H-UV dryer on System 38S
The development concept that produced Komori's H-UV web presses consisted of three elements. First, achieve a radical reduction in paper waste at press start-up. Second, provide sheetfed-level print quality. And finally, design a press that benefits the environment.
In the past, a major problem for web offset presses has been start-up waste due to the necessary adjustments for paper shrinking and web meandering as a result of the heat of the dryer. To dramatically cut paper loss, the hot-air dryer that is normally configured with web offset presses has been eliminated along with the chill stand and the complex configuration of chill rolls in the chill roll assembly. This reduces the total length of the press to two-thirds that of a conventional web press. When specified with a sheeter, the height of the machine is just 2.7 meters, making it suitable for installation in the pressrooms of most sheetfed users. This compact, space-saving arrangement solves the problem of unstable web behavior, which is exacerbated by a longer paper path.
The new H-UV-equipped presses take the advances of the KHS-AI quick start-up system and the AI-Link integrated control system a step further. By incorporating a special H-UV mode that combines the stable travel of the paper afforded by the shorter paper path with changes to the acceleration gradient and the printing on-off timing, the H-UV presses significantly slash start-up paper loss and also shorten start-up time.
While a KHS-AI-equipped conventional web offset press typically has start-up waste of 800 to 1,000 copies, the new H-UV web presses reduce this to just 200 copies. This results from optimal web tension and precise control of not only color but also cutoff position and cross direction. The result -- the most powerful short-run, quick-turnaround web solution in the world.
Sheetfed-level quality by design
One key to achieving the print quality of sheetfed presses is related to the moisture content of paper. The hot-air dryer of a conventional web press typically reduces the moisture content of the paper, resulting in wrinkling of the web. These problems, as well as postpress issues such as smearing, are suppressed by Komori's H-UV web technology. Since moisture content of the paper before and after drying is identical, even the problem of static is eliminated.
In addition, there is no dry-down with H-UV's instant drying and densities are consistently on target, so print quality is comparable to that of a sheetfed press.
Environmental benefits
The green credentials of H-UV System Series web presses are very substantial. The reduction of energy usage is significant because the hot air dryer and blower are completely eliminated. And CO2 emissions are reduced due to less makeready waste. In addition, since UV ink is used, VOC emissions are zero.
H-UV is, of course, an entirely ozone-free process, which is a plus for the environment and removes the need for an exhaust duct. And even though the rate of production is two to three times greater than that of a sheetfed press, only one H-UV lamp per side is needed, which lowers both initial and running costs.
H-UV lamp performance
For H-UV drying, the 160 W/cm lamp enables production of 30,000 impressions per hour. This is possible because of the construction of web machines. Compared to sheetfed presses, a significant advantage of the webfed design lies in the method of sheet transport. In a sheetfed press, one edge of the sheet is held by the grippers, whereas with a web offset press, the paper of the web is a single connected roll, allowing the web to be held under tension in a stabilizing, defined way. Thus web presses are fundamentally more suitable for higher printing speeds than sheetfed presses. This also allows the H-UV lamp to be positioned closer to the paper surface than in the case of a sheetfed press. Along with a newly designed reflector, the lamp yields a radiation intensity that is 30 percent higher than the equivalent lamp in a sheetfed press.
The numbers behind the story
A four-color sixteen-page System Series press configured with a sheeter is just 16.5 meters long, 7.8 meters shorter than a similarly specified conventional web using solvent-based ink. The System 38S press accommodates web widths of 625-965 mm and may be specified with a cutoff length of 578, 598 or 625 mm. In addition, a version of the System 38S for book printing has a cutoff of 638 mm and a web width range of 880-924 mm. The System 35S handles web widths of 620-880 mm and provides a cutoff of 546 mm. The paper stock range for both presses is 40-130 gsm. Komori's System Series H-UV web presses are shipped with fully automatic plate-changing (Full-APC) as standard equipment for ultra-short-run work.
Transforming powers
Komori's System web offset presses have been the gold standard in the commercial web industry for three overwhelming reasons: high quality, high productivity and high added value. The KHS-AI and AI-Link mechatronics work together with Komori technologies such as Full-APC to make the System 35S/38S the definitive web offset platform for short-run, fast-turnaround work. Now configured with the H-UV drying system, these presses offer an entirely new range of possibilities to sheetfed users. Instant drying without a dryer, of course, but also the stunning impact of wrinkle-free H-UV printing. Ozone-free, powderless, free of the characteristic odor of UV, space-saving, energy-saving, and available with the full range of Komori options that have made the System Series machines the preferred web solution worldwide. Sheetfed-level quality with web productivity. This innovative development is perfect for sheetfed users who wish to implement a Web-to-print or gang-run printing business model -- the competitive strength of an H-UV-enabled System 35S/38S changes all the equations. The sum of Komori's development achievements and expertise in a design aimed squarely at the pinnacle of printing. The Komori H-UV System 35S/38S web offset presses.