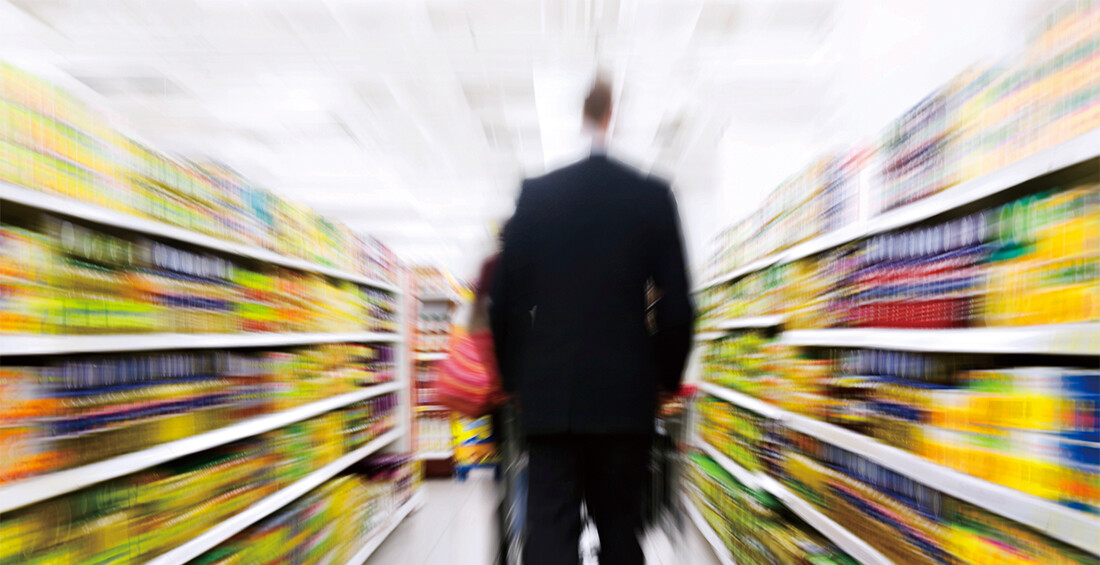
Ink on board is the crucial process that underlies the production of the millions of packages that billions of consumers encounter every day. Packaging is art, design, business, chemistry, technology, engineering, marketing and so much more. Komori is determined to cover all the bases.
The Lithrone GX40 Flagship Press
Packaging is one of the hottest segments of the printing industry for thousands of reasons but none more compelling than the package's position squarely on the pulse of the vast majority of consumer purchasing decisions: point of sale. The final point of communicating to the customer. And because packaging has such a crucial role in the marketing mix — in defining the character of new products and in creating brand identity and shelf impact among all product groups — the packaging producer must be able to use new materials, deliver new shapes, print more colors in greater definition and deliver shorter runs. And do this all economically.
Packaging is also dynamic — constantly changing to the rhythm of the ever-bustling marketplace. Eye-catching and colorful designs enhance brand awareness and stand out on the shelf. And today, social trends are driving packaging production requirements. Smaller pack sizes for single-serving and on-the-go use accommodate lifestyle changes and evolving demographics. Increasingly, packages for food and medicine must ensure traceability and use low-migration ink. Environmental concerns demand production that affords sustainability and meets eco-sensitive regulations. Braille is required on some packages — and a desirable option on many more. High added value printing is insisted on not only for product differentiation but also to prevent counterfeiting.
Package printing involves meeting many unique requirements perfectly. Stock tends to be high-end heavy paper or board, meaning waste cannot be tolerated. Packaging is a part of the distribution system, so nonstop around-the-clock operation is often the norm. And, more than any other stakeholder in mass production, brand owners insist on dead-on color accuracy and print quality. This makes state-of-the-art color measurement and print quality assessment systems absolutely essential.
Lithrone GX40: unsurpassed for packaging
For the total look and feel of packaging in the 21st century, Komori is more and more the preferred choice for its end-to-end solutions to the specific needs of the industry. No press on the market approaches the Lithrone GX40 in high added value printing and special effects capabilities. The machine was literally designed from the ground up in close collaboration with package printers. It incorporates the mechanics, the electronics, the automation and the software that will help packaging producers thrive in this intensely competitive field.
The mechatronics products centered on the KHS-AI integrated control system for quick print start-up ensure changeovers and makereadies that no other system can provide. Year in and year out, makeready is ultraprecise, fully automated and lightning quick. Color and register are on the mark. And waste sheets are a nonissue. Print quality is designed into the press — from the flawless sheet transport to the world's most innovative inking system. And it is inspected, measured and evaluated to make certain no defective sheet ever reaches the delivery pile.
Lithrone GX40RP: two sides on one pass
The Lithrone GX40 and its state-of-the-art peripherals are hardly the only weapon in Komori's arsenal. A sister machine, the Lithrone GX40RP cardboard specification front/reverse multicolor offset printing press, is a dedicated double-sided machine that will lay down up to 10 colors on two sides in one pass without flipping the sheets. It is supported by the same superb lineup of mechatronics options and peripherals as the Lithrone GX40 and can be specified for either UV or H-UV printing.
The real difference: very special intangibles
But the real key to Komori's credentials in package printing lies elsewhere. It's the people. The Komori designers who render custom-configured presses for unique applications with every ounce of technical know-how in their power. The Komori service technicians who yield to no one in dedication. And the vast experience and expertise wielded by the people who belong to the only company in the world manufacturing sheetfed, web offset, intaglio, gravure offset and digital inkjet presses as well as a growing range of prepress and postpress equipment and printing supplies. The specifications provide the facts, but these intangibles — Komori people and their commitment to getting it right — are the reasons printers stay with Komori.
Tsukuba Open house draws a crowd to see high-spec packaging machines
Printers from around the world visited the Tsukuba Plant on March 12 to discover Komori's latest solutions for the growing packaging market. The solutions were many but they could all be summed up in one word: automation. Automation of printing processes such as makeready, automation of materials handling, and automation of total print quality control and assessment. But this open house event covered more than technologies and products. The day's proceedings reacquainted the visitors with Komori and provided opportunities to compare notes with packaging producers in other markets and other countries. The buzz from this chemistry grew throughout the day and peaked during the nighttime festivities.
The printers were welcomed to Tsukuba by Toshiyuki Tsugawa, Operating Officer and Group General Manager of the Overseas Sales Group, who pointed out the extent of Komori's commitment to this rising market segment. Following a showing of the latest corporate video, the day's main presentation, 'Komori Packaging Solutions,' was delivered by Doug Schardt, Product Manager from Komori America Corporation.
Rundown on the packaging industry
Mr. Schardt's briefing pinpointed the industry trends that all printers in this market face and highlighted the main elements of the day's demonstration, specifically those that impact profit and ROI. Market needs in this field are much the same as in other segments of printing: shorter runs, tighter turnarounds, and greater diversity. Komori's answer is PackagingOnDemand: the Lithrone GX40 and Lithrone GX40RP, in particular, supplemented by half-size offset machines, digital printing systems, and a multitude of peripherals and PESP products that add up to a total, customizable approach.
Priority on distinctive performance
Emphasis was on the highly evolved technologies incorporated in the KHS-AI quick start-up system, the PDC-SX scanner and the PQA-S inspection system — the key mechatronics that distinguish Komori from other manufacturers. Smart Sequence for preprogrammed optimization of job changeover items, and Smart Feedback for automation of changes after makeready. The key strengths of the Lithrone's robust inker and Komorimatic dampening system. And above all, the higher level of performance made possible by the tight integration of these systems and technologies in Komori's flagship machines.
Demos pack a punch
Following lunch, Schardt offered a master class in running jobs on the high-spec Lithrones. The Lithrone GX40 with coater printed 500 sheets of 0.35 mm stock in six-color UV with gloss coating and then, following changeover, output 2,000 sheets of 0.45 mm stock. The delivery pile was changed during the second job by the logistics system with no change in the production speed. The Lithrone GX40RP H-UV also printed two jobs, the first 4 over 2 and the second 4 over 1. This demonstration spotlighted the exceptionally smooth sheet transfer offered by the reverse printing press because the sheets are not flipped, which is especially important with costly heavy stock. In addition, the configuration requires no tail edge margin, thus improving the economic picture. The six-color Lithrone S29 with coater rounded out the demonstrations, printing 200 sheets of 0.3 mm board at 16,000 sph and then following up with 200 sheets of PET at 10,000 sph.
After these demonstrations, the group toured the recently remodeled Komori Graphic Technology Center and then returned to the conference room for a seminar on advanced printing materials.
A powerful brew
The participants then decamped to a downtown hotel for a party where Chairman Yoshiharu Komori greeted everyone. The mix of nationalities, languages and specialties made for a powerful brew, and printers networked until the magic hour, when the buses arrived for the trip back to Tokyo. The busy day had been worth it.
Full-spec Lithrone GX40
Highlights of the Action
The demonstration of the six-color Lithrone GX40 with UV and coater was the highlight of the day. The reason scores of printers gathered at the Tsukuba Plant. This was the machine that would — for many — set the course of their company's future.
Schardt briefly oriented the group to the position of the various systems covered in the presentation before outlining the jobs — the first, a 500-sheet run on 0.35 mm board for medicine, and the second, a 2,000-sheet run on 0.45 mm board for confectioneries. The speed of start-up, operation and changeover was so fast that many points could only be mentioned in passing. A quiet murmur could be heard as the mighty machine hit its 18,000 sph maximum printing speed. The run seemed to have barely begun when the press decelerated and began its preprogrammed changeover tasks, changing plates automatically and almost soundlessly. The second run began, and the printers seemed even more conscious of concepts — stability, quality and productivity — that heretofore had been only elements of the presentation. And then it was over. The printers reached for printing samples to take home and swarmed up on the machine to verify different aspects.
The eight-color Lithrone GX40RP reverse printing press — a one-of-a-kind machine manufactured by no other maker — printed both sides in one pass using Komori H-UV ink. High-precision CCD cameras inspected both sides simultaneously. Reliability and predictability incarnate.
And then the six-color Lithrone S29 performed. Flawlessly laying down ink on a clear plastic substrate. And the demonstration was over. Stunning results on a variety of difficult jobs. Package printing perfection.