Boutaux Packaging and the magic of H-UV
France, Boutaux Packaging | Lithrone G40 [GL-540 H-UV]
01 August 2017
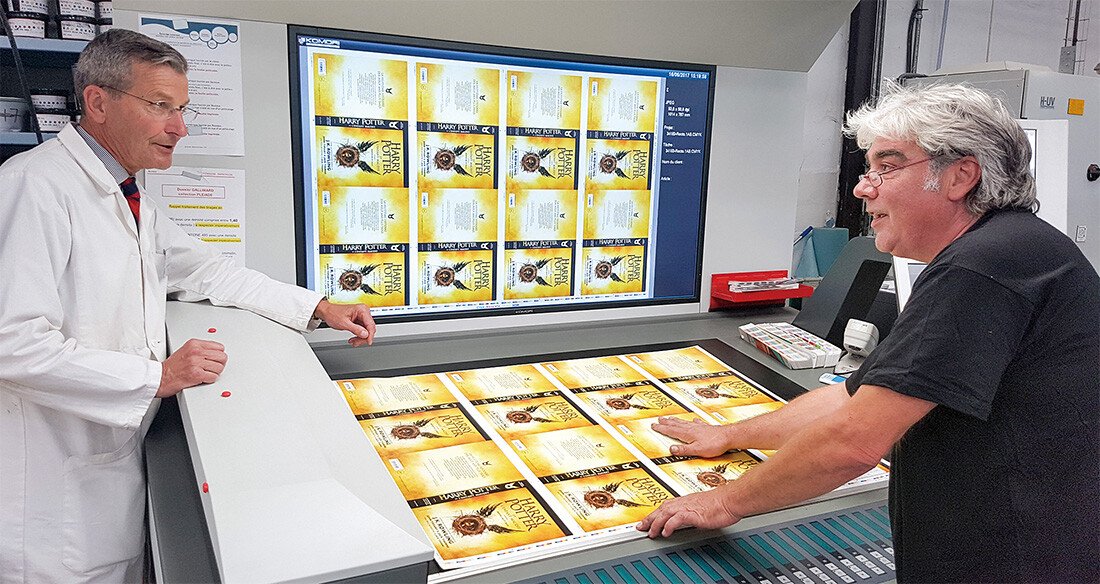
"At Boutaux, beauty is all we know, and difficulty is what drives our creativity." Such is the philosophy that motivates Géry Bailliard, President and CEO of the Boutaux Packaging printing company, which operates out of an 8,000 square meter facility in Val-au-Perche in the Orne region.
Géry Bailliard (left) says the Lithrone G40 H-UV was vital to the success of the Harry Potter project
The company's historic client base is made up of publishers, and its work includes the cover of the Prix Goncourt 2014 winner, Cry, Mother Spain (Pas Pleurer) by Lydie Salvayre, as well as the cover of the latest Guillaume Musso, An Apartment in Paris (Un appartement à Paris). Then, of course, there are the slipcases used to protect the precious volumes of the classic Pléiade collection, which Boutaux has been producing for 20 years. The publishing market accounts for 60 percent of its business, but it has also made a name for itself in cardboard packaging with high added value for the cosmetics/perfume, specialty foods, high tech and fashion industries.
The more complex, the better
Wines and spirits, a promising target segment for Boutaux thanks to the broad spectrum of grammages offered by its brand new Komori H-UV press
Boutaux Packaging has become a specialist in the use of high-tech processes: soft-touch lamination, spot coating, multilevel embossing, hot foil stamping, screen printing and foil imprinting with opaque white. The unusual is part of its day-to-day work. The company never shies away from a challenge. For instance, it created the Marsupilami collector's set, printed on flocked luxine for an authentic "furry" feel, which won the Oscar de l'Emballage award in 2013.
The Lithrone G40 H-UV: a strategic investment
"We had two aging presses. In 2016, we decided to replace them with a Komori H-UV press," explains Mr. Bailliard. "By expanding our creative possibilities, H-UV technology enabled us to move upmarket, which boosted our strategy to win new markets. It was also a good fit with our commitment to protect the environment. We opted for a five-color Lithrone G40 H-UV press with PDC-SX and KID, speculating that the increase in productivity would offset the purchase price. The gamble paid off — the makeready and production times are shorter, and the fact that we no longer have powder improves the quality of our products, eliminating the risk of smearing. Above all, thanks to instant drying, finishing can be done immediately."
The two Harry Potter wizard challenges
The first Harry Potter challenge was technical, relating to the cover of the eighth installment: "We had to print in gold directly on the back and make provision for four refining passes on the front. With its immediate drying, H-UV was invaluable in meeting this challenge, particularly given the extremely tight deadlines. I'm certain we would never have won the international call for tenders had we stayed with traditional offset printing," reveals Bailliard. However, the second challenge took place in a space-time continuum. In June 2016, Boutaux Packaging knew that it would have to print 650,000 Harry Potter covers that August, with the Lithrone having been in service for just one month. Furthermore, neither publisher nor printer had any room for error.
An alliance between manufacturer, printer and publisher
From left: Géry Bailliard, President and CEO; Gilles Douyer, Production and IT Manager; Michel Malaganne, responsible for QSE and R&D; and Jean-Marie Guibert, responsible for studies and ISO 12647-2
In preparation for this project, Bailliard contacted Komori well in advance: "Our four operators had a week's training at the Komori Graphic Center-Europe in Utrecht, the Netherlands, before participating in a six-week program here with one trainer and several Komori fitters. I took on some temporary employees to do the day-to-day work on the old press because I wanted my operators to devote themselves fully to the new Komori. As an extra safeguard for the Harry Potter project, I brought in an operator specialized in Komori H-UV presses. The Komori trainer was also there for added peace of mind. I informed Gallimard, the publisher of the Harry Potter series, of all this from the start, and they were reassured by the Komori/Boutaux Packaging alliance. It was thanks to this mutual trust that we made a success of this exacting production."
A vector for diversification
"Every day, we discover new possibilities with this H-UV technology," he explains enthusiastically. "We are taking orders in the spirits sector, since we can now work on 650 g cardboard without the need for litho-laminating, which makes us more competitive. Recently, we were approved by Cosmetic Valley in Chartres, as we are ISO 9001 and ISO 12647-2 certified and, thanks to this equipment, we will now be able to create innovative packaging for this high-end perfume manufacturer's customer base." It could be that this machine has magical powers!