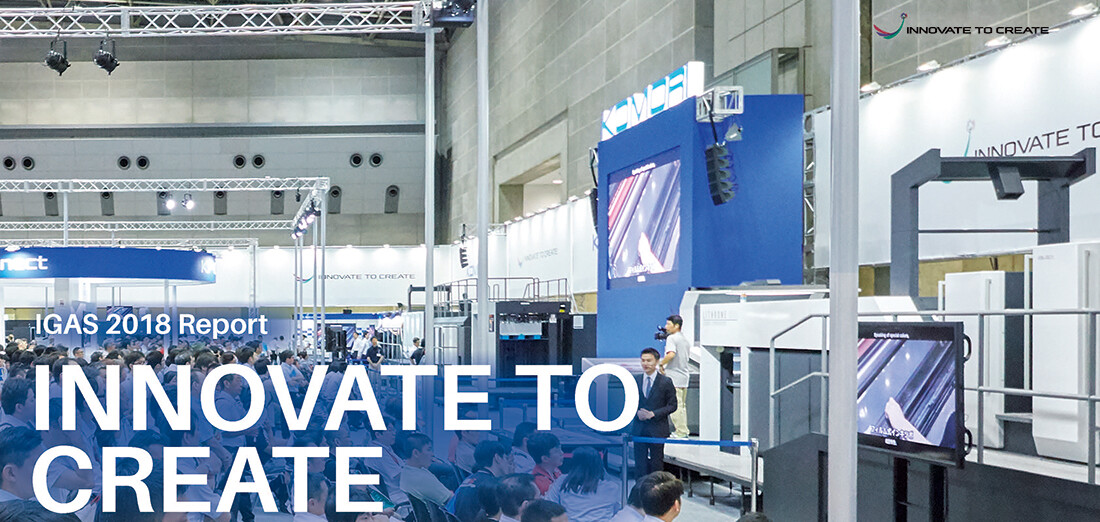
IGAS 2018 took over the Tokyo Big Sight from July 26 to 31, 2018, for an incredible show. The Komori booth realized a printing plant with processes linked by connecting the latest machines with KP-Connect Pro. Visitors were totally captivated.
IGAS2018 overview video
Printing plant optimization by Connected Automation
'Innovate to Create' was the expression most overheard in the Komori booth. That is, the shift from 'how to make' to 'what to create.' Komori intends to lead the change from using human abilities in manufacturing to mobilizing them in the creative realm — where people produce added value. Connected Automation is the approach for realizing this change, and the Komori booth was its embodiment.
Connected Automation is the concept of linking prepress, press and postpress and optimizing work throughout the plant by automated production facilities. Based on this idea, Komori is advancing development in a range of fields. The objective is to achieve laborsaving and unmanned operation in the transfer of job data between processes and in the materials flow in the plant, and to implement centralized control of all processes.
At IGAS, Komori materialized a smart factory. By connecting 10 machines with KP-Connect Pro in the center of the booth, the entire booth became a printing plant.
Factory signage showed operating information in real time, enabling visitors to see the centrally controlled action throughout the plant.
Demonstrations Spotlight Operator Action
Lithrone GX40RP and Apressia CTX132
Demonstration of automatic operation by Autopilot and Parallel Makeready.
The Lithrone GX40RP showed automatic performance of three jobs.
The background to Connected Automation is the problem of securing manpower. Worker shortages are due to difficult working conditions such as long shifts and night shifts and a significant reduction in the working population in some countries. It is critical to improve labor productivity in the printing workplace. By exhibiting and demonstrating machines that advance automation and laborsaving, Komori showed how the workplace and the operator's job will change.
Autopilot is the automatic operating system that completes everything from test printing to production printing nonstop. And Parallel Makeready performs the job changeover processes in parallel and sharply reduces preparation time. Equipped with these latest technologies, the Lithrone GX40RP (eight-color 40-inch front/reverse multi-color offset printing press equipped with H-UV L (LED)) received the job ticket for automatic operation from KP-Connect Pro and performed a total of three jobs in 10 minutes: ganging of an imposition of various sized images and two 16-page A4 catalog jobs. Fully automated printing.
The Lithrone GX40RP first laid down four colors, instantly dried with H-UV L (LED), then printed four colors on the reverse side and instantly dried with H-UV L (LED). Powderless one-pass printing and instant drying with the work ready for immediate finishing. Samples from production printing were passed out for checking.
The point of the demo was the changeover from one job to the next. Parallel Makeready handled three processes simultaneously — blanket washing, plate changing and pre-inking — letting the audience experience the considerable reduction in makeready time. The 4K camera-equipped PQA-S V5 Print Quality Assessment System began color control and automatic register adjustment after the completion of plate changing by A-APC (asynchronous automatic plate changer) at the start of production printing. The automatic adjustment of densities and register wowed the crowd.
The demo introduced the tie-up with the Apressia CTX132 (programmable hydraulic clamp cutting system) equipped with an automatic paper transport system, which was installed across from the Lithrone GX40RP. The product slip for the first job output from KHS-AI along with the printed sheets was passed to the Apressia CTX132 operator, who scanned the two-dimensional code on the product slip with an iPad camera. The processing data created by Equios was automatically passed to the Apressia CTX132, and preview information, cutting dimensions and cutting order were automatically set. The automatic links between processes implemented by KP-Connect Pro's Connected Automation were particularly impressive.
KP-Connect
KP-Connect in the center of the Komori booth. Factory signage indicating operating status shows all machines are connected with and centrally controlled by KP-Connect Pro. A mini-seminar introduced KP-Connect features.
Lithrone GX40, Apressia DC105 and Apressia MB110E
The Lithrone GX40 showed six-color printing, drip-off effect by coater varnish, instant drying by H-UV L (LED) curing system, simultaneous blanket washing, ink roller cleaning and asynchronous automatic plate changing, plus short job changeover including color changes by a newly developed film-type ink fountain. Following printing, demonstration of cutting by the Apressia DC105 and blanking by the Apressia MB110E, both seamlessly linked for optimized production through Connected Automation.
In addition to the Lithrone GX40RP, other demonstrations of Connected Automation were presented. The Lithrone GX40 (six-color 40-inch offset printing press with in-line coater equipped with H-UV L (LED)) was linked with the Apressia DC105 (automatic flatbed die cutting and creasing machine) and the Apressia MB110E (high performance blanking system). In the demonstration, the operator checked the job ticket sent from KP-Connect Pro and simply pressed the start button. Packaging sheets with drip-off effect printed by the Lithrone GX40 were then cut by the Apressia DC105 and blanking was performed by the Apressia MB110E. Similarly, following wide color gamut digital printing by the Impremia IS29 (29-inch sheetfed UV inkjet digital printing system), the work was sent to the Highcon Euclid to be made into final products by creasing, cutting and fine processing.
High Interest in Machine Performance
Impremia IS29 and Highcon Euclid
Demonstration of wristwatch package production. Output of seven special colors at 3,000 sph on Impremia IS29, immediately followed by creasing and laser cutting on Highcon Euclid, showing capability with short turnaround package jobs.
The Impremia IS29 introduced in the demonstration of Connected Automation drew remarkable attention. A B2 inkjet digital printing system that prints directly on a wide range of stocks and performs double-sided printing, the Impremia IS29 is Komori's answer to the question: What is essential in a digital printing system for professional printers? Ordinary offset printing stock can be printed as is, no precoating is necessary, and the system produces high print quality approaching offset. Equipped with a sheet reversal mechanism that allows both straight and double-sided printing and offering the ability to start postpress work immediately after printing thanks to instant drying, the Impremia IS29 is seeing an upsurge of installations as demand for small lots and short turnarounds increases.
The Impremia IS29 introduced in the demonstration of Connected Automation drew remarkable attention. A B2 inkjet digital printing system that prints directly on a wide range of stocks and performs double-sided printing, the Impremia IS29 is Komori's answer to the question: What is essential in a digital printing system for professional printers? Ordinary offset printing stock can be printed as is, no precoating is necessary, and the system produces high print quality approaching offset. Equipped with a sheet reversal mechanism that allows both straight and double-sided printing and offering the ability to start postpress work immediately after printing thanks to instant drying, the Impremia IS29 is seeing an upsurge of installations as demand for small lots and short turnarounds increases.
The Impremia IS29's power goes beyond just handling short runs with quick turnarounds. In the demonstration, it presented new printing possibilities by output of a photo collection with variable printing and a wide RGB color gamut using a book-block imposition, cards on a white plastic substrate, and packaging that introduced unrestricted reproduction of special colors. Nearby stood an exhibit of products printed by customers internationally who have installed an Impremia IS29. The wide range of applications evoked great interest.
At IGAS 2018, in addition to the Apressia CTX132 cutting system and the Apressia MB110E blanking system, the Lithrone G37P (eight-color 37-inch convertible perfecting offset printing press equipped with H-UV L (LED)) and the Lithrone G37 (four-color 37-inch offset printing press equipped with H-UV) were exhibited as the newest products.
Lithrone G37P
Demonstration of double-sided one-pass printing with instant drying by H-UV L (LED). Explanation of density and register checking by PDC-SX spectral print density control as well as color control by PQA-S V5.
Featuring instant curing with H-UV L (LED), high print quality and perfecting printing, the Lithrone G37P enables one-pass double-sided printing. In addition, its primary attraction is responsiveness across a wide range of work, from double-sided to multi-color straight printing, including special colors, by changeover from perfecting to straight mode. The demonstration showed a test printing sample scanned by the PDC-SX Spectral Print Density Control, with both densities and register checked with one measurement for feedback to the press.
The outstanding characteristic of the Lithrone G37, a 37-inch machine, is its ability to print 8-up A4 impositions, thus reducing plate costs compared to a 40-inch press. At IGAS, the Lithrone G37 was equipped with the powderless H-UV instant curing system, Parallel Makeready for simultaneous blanket washing and pre-inking, and the Full-APC Automatic Plate Changer. This press is characterized by the expression 'everything just right.'
Next-generation machines ready for immediate application in a variety of printing scenes, the Lithrone G37P and the Lithrone G37 drew highly appreciative audiences.
Komori-Kare: Materials, Service and Maintenance
Komori provides the perfect support system for customers. The optimum materials and maintenance for maximizing the performance of presses were introduced. In the Komori-Kare and Komori Ecology areas, materials and maintenance optimized to derive maximum performance from products were shown and representatives answered questions from showgoers.
A lineup of all the equipment and materials necessary for printing, including retrofit products and K-Supply products, was also displayed. An easy-to-understand exhibit showed consumables such as inks, rollers, blankets and pre-soaked cloths. Here, a proposal area presented routine working improvements as well as points for restoring performance from the effects of aging. Also, the installation benefits and case studies of retrofit products together with a mini-seminar introducing the voices of customers were presented.
During the six days of IGAS 2018, Komori's vision for a dynamic printing industry driven by kando innovation was unveiled. Innovate to Create — the future with Komori.
-
By just scanning the pro-duct slip with an iPad, pre-view information, cutting dimensions and cutting order are automatically set on the Apressia CTX132.
-
-
-