Apressia CT115 changes the game at Bootyman
UK, Bootyman Printers | Apressia CT115
01 December 2018
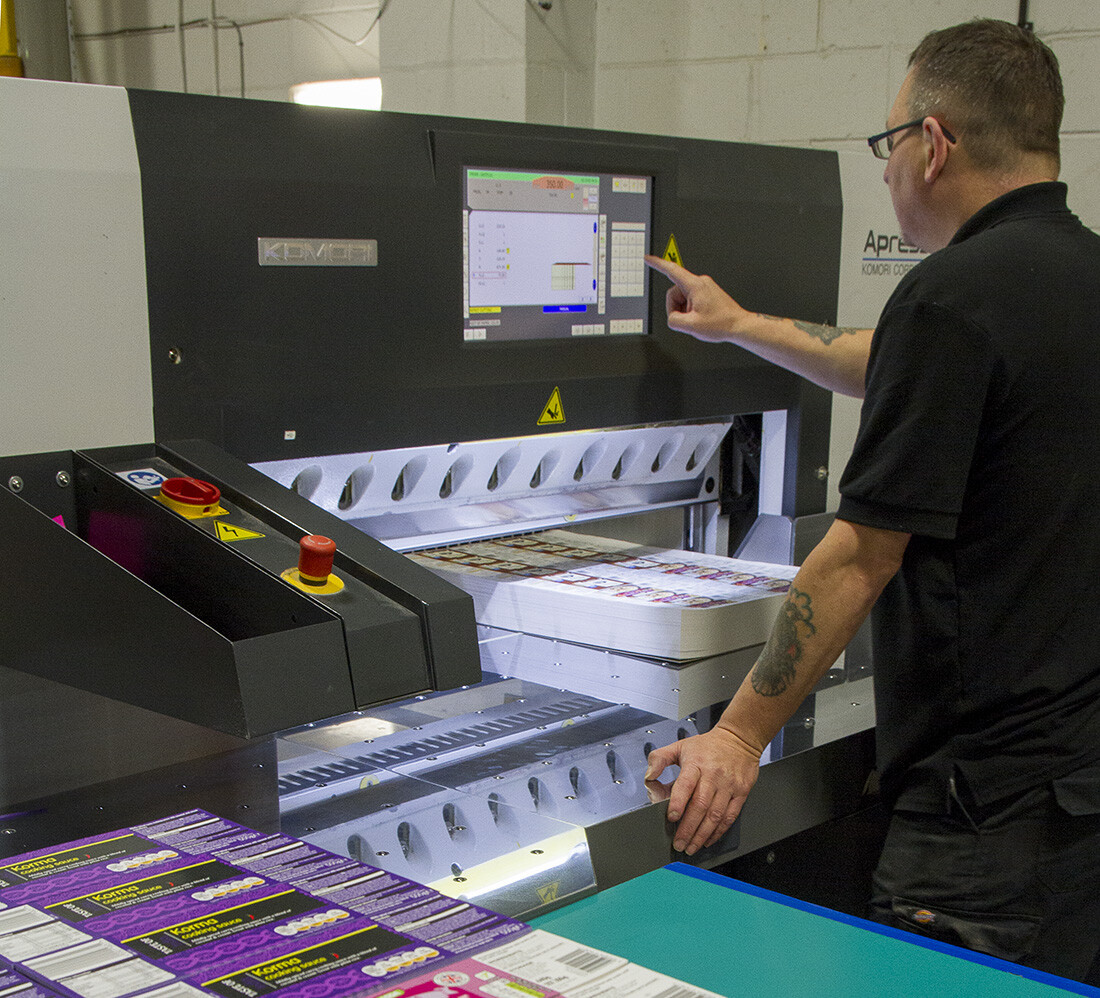
The increased volume of wet glue labels produced on its two new six-color Lithrone G29s has created the need for the latest cutting-edge technology in the form of the Apressia CT115 at the UK's Bootyman Printers.
Bootyman Printers was founded by William Bootyman 104 years ago in the port city of Kingston upon Hull as a jobbing printer, initially producing stationery, small format leaflets and documents for the many local retail and commercial businesses around the city and beyond in East Yorkshire, England.
Today annual turnover is approach-ing €4 million as Bootyman has become one of the UK's leading suppliers of wet glue/flexo labels and folding box board packaging, which it produces for many of the UK's major brands.
The increased volume of print progressing through to the finishing department over the last year, especially sheets of wet glue labels, highlighted the need to upgrade guillotining productivity and led to the subsequent installation of the Komori Apressia CT115. Managing Director Andy Binks explains: "We now produce 360 million wet glue labels a year, all of which involve guillotining. With our previous cutting machine, downtimes for programming, maintenance and routine blade replacements were in danger of creating a bottleneck as our workload stepped up."
"We conducted tests at Komori Graphic Center in Utrecht, where our guillotine operators were given free rein on the machine. They were especially impressed by its continuous productivity features and fast maintenance mechanisms such as the click in-click out cutting strip replacement system, knife exchange automation and conveniently located adjustment controls."
"Guillotining, by its very nature, is an intensive job and so other operator-friendly aspects such as the programmable clamp pressure and electronic back gauge adjustment also impressed our operators. The large digital touch screen, pre-programming and memory systems were also of key importance to us, as we cut to so many different dimensions and also handle many repeat and complex jobs."
He concludes: "Now that the Apressia is installed and in operation at least 16 hours a day, five days a week, we've realized just how much the latest Komori cutting technology contributes to our throughput."