W2P Production Expansion: Printnet strategically installs eight double-sided, one-pass presses
Japan, Printnet | Six Lithrone GX40RPs [GLX-840RP H-UV]
28 March 2022
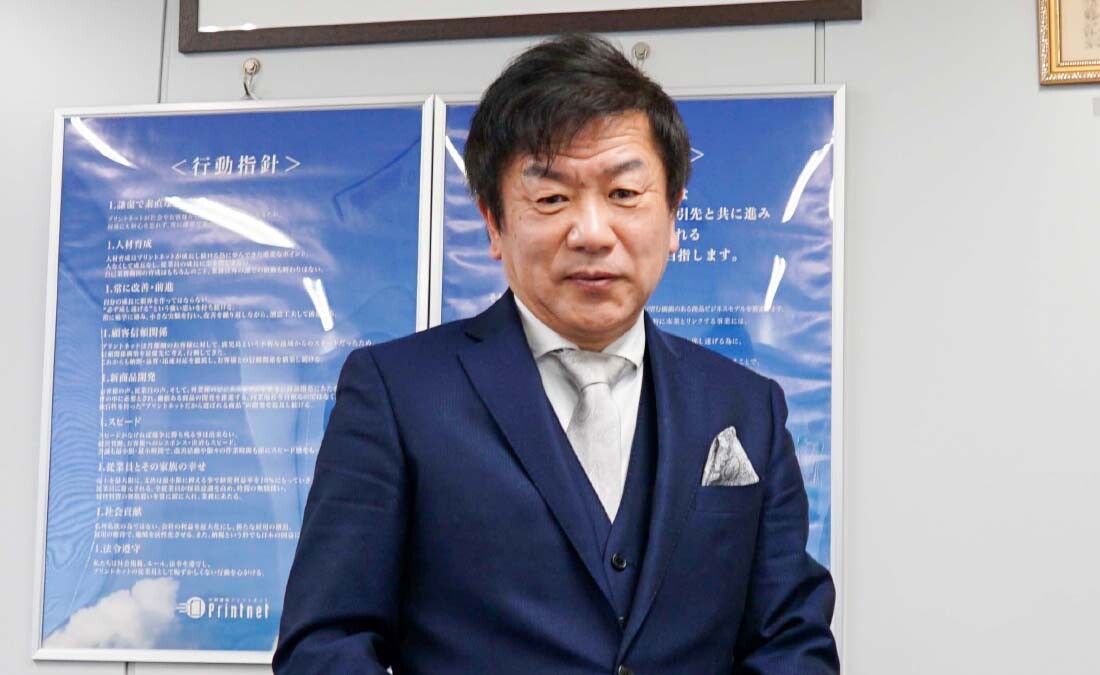
Printnet Co., Ltd,, a fast-growing company in the web-to-print (W2P) sector, has greatly expanded its production capacity by installing eight double-sided, one-pass presses over a two-year period. These consist of six double-sided presses, one web offset press, and one digital press all from Komori. The two Lithrone GX40RPs 40-inch double-sided presses operating at the Kyushu plant have combined to achieve an astounding monthly production output of 8.95 million sheets.
“To strengthen our web-to-print printing business, which requires high production, we have installed state-of-the-art equipment with high production efficiency.” —Yoichi Odawara, President and Representative Director
On Press interviewed President and Representative Director Yoichi Odawara, Kyushu Plant Manager Shigeki Taira, and Printing Section Chief Kazunari Yamamoto about the strategy behind the installation of the double-sided, one-pass presses, and in particular, the deciding factors behind the introduction of the RP presses and their effectiveness in operation.
Shigeki Taira, Plant Manager, Kyushu Plant (left)
"Those of us on the shop floor are closest to the product. I believe that the awareness and actions of quality assurance by everyone in the plant will lead to the next order."
Kazunari Yamamoto, Printing Section Chief, Kyushu Plant (right)
"The regular maintenance we do with Komori Service has been very helpful in reducing the amount of start-up paper waste."
Most important strength: customer service centered on production and quality
Printnet's W2P business provides unique services in pursuit of customer convenience. "We have two websites, Printnet, a W2P site for general customers, and PrintPro for printing companies and designers. We are raising customer satisfaction by providing excellent service at our customer center," says President Odawara. Production is handled by two plants, in Kyushu and Tokyo West, which serve western and eastern Japan, respectively.
Due to the increase in the volume of orders, Printnet installed six Lithrone GX40RP double-sided offset presses from 2017 to 2019, two in the newly constructed Kyushu Plant and four in the Tokyo West plant.
Odawara explains the reason behind the installation of all six RP machines: "We had been using Komori RP presses for many years and experienced their excellence. The RP press design offers tremendous cost benefits when printing on A1 paper because of the margin advantages. Every feature on the latest presses contributes to extremely fast changeovers, so we expected a major improvement in production." In particular, the presses must be running constantly to meet the quick deliveries in the W2P business, so maintenance service after installation was an important point in the selection of the manufacturer, he adds.
Plant Manager Taira says, "The RP presses offer superb front-to-back register accuracy even in high-speed printing, and there are no marking issues such as scratches. In addition, since margins on the ends of the sheets are not necessary and saddle-stitched A5 booklets can be easily imposed on A1 paper, paper loss is reduced. Furthermore, compared to our previous single-sided oil-based presses, double-sided printing with instant cure H-UV ink no quality problems such as set-off, and there is no waiting time for postpress processes or shipment. As a result, we are able to accept some same-day quick-delivery jobs up to 4:00 p.m., which is two hours later than before.
Monthly production of 8.95 million sheets by two Lithrone GX40RP presses equipped with the latest control systems
From October 2021 production results: Actual screen of KP-Connect showing the highest average weekly operating rate. The parallel control system allows us to complete blanket washing, plate changing, and pre-inking simultaneously in two minutes, which saves a lot of time," (Taira)
Regarding efficiency, Taira says, "Since feeding and delivery are both stable at high speeds, we always print at 14,000 to 15,000 sheets per hour, and we teach new operators to run at this speed right from the beginning."
"Previously, blanket washing, plate changing, and pre-inking took about 10 minutes, but since Parallel Makeready performs these tasks simultaneously, our machines now are ready in about two minutes. I think production efficiency has been changed greatly by this," says Section Chief Yamamoto.
The background to these results is the presence of KP-Connect, Komori's solution cloud. "KP-Connect data is very useful for visualizing production. In checking a variety of production parameters, we pay close attention to the hourly production volume, the daily operating rate, and the amount of waste paper. We have set high production targets, and in terms of throughput, for example, the best recent monthly record for the two Lithrone GX40RPs combined is 8.95 million sheets. Operating results are high, with a weekly average operating rate of 53 percent and a maximum single-day record of 58.3 percent," says Taira.
Regarding the visualization of production by means of KP-Connect, Odawara says, "We carefully watch the volume of paper waste. The Kyushu and Tokyo plants report production results to each other at monthly meetings, including paper waste, and this competition leads to improved productivity," emphasizing a friendly rivalry between facilities. He also mentions that KP-Connect's visualization function is very useful in the improvement of bottlenecks such as determining the cause of downtime.
Various automatic functions equipped on the RP presses enable not only production but also quick start-up while ensuring print quality. "Smart feedback is especially advantageous. By fully using KHS-AI and PDC-SX, color comes up quickly and quality is guaranteed. Test printing is done just one time with a basic run of just 30 sheets," says Yamamoto. "It is important to always keep the machine in good condition, and to do that we have a great maintenance program in conjunction with Komori Service," he adds.
"For quality, both the Kyushu and Tokyo plants have acquired Japan Color certification and we basically control using this as the standard. Unification and standardization of procedures with PDC-SX for color control, which is equipped in both plants, leads to shortening of operator training," says Taira.
"With the remarkable automation of press operations by printing systems such as KHS-AI, experience has become unnecessary. In the Kyushu Plant, operators with less than two years of experience at the new plant can nearly be press operators," says Yamamoto.
Employee autonomy and more automation to further grow the web-to-print business
The printing team at the Kyushu Plant. "By raising printing productivity, everyone has become more skilled and capable of performing multiple processes, and we are also supporting postpress processes. As a result, employees have developed a sense of helping each other, and this has led to plant-wide teamwork to achieve results together." (Taira)
Odawara comments on the future strategy: "In the future, we will continue to improve our services and deliver better products with shorter turnarounds based on the motto of "with modesty, we will advance with our customers," which is our company policy. In the mid- to long-term, we aim to establish our solid cost advantages and become the only company in this field. At the same time, there are high expectations for more automated printing presses, and we would like to further grow our field of expertise by pursuing more and more efficient production."
The latest Lithrone GX40RP at Tokyo West (Plant No. 2) is equipped with the world's first "Autopilot" function for automated one-man operation, enabling the press to automatically make quality inspection decisions in addition to color and registration adjustments. The result is zero quality issues. Komori will continue to strive to minimize paper waste and bring the system closer to Printnet's ideals.
Kyushu Plant