Postpress
Process Streamlining: Jogging, Cutting and Pallet Loading
Making processes more efficient and smart is an enduring print shop theme, so let's look again at the cutting process. Specifically, let's consider the effects of heavy labor on people and stress on the paper.
For instance, recently more companies are doing in-house the job of cutting printing stock before printing. For this, the cutting process must be positioned with an important base point for loading paper onto the press. This is because the first pallet after cutting is set on the press as is. If this is not satisfactorily accomplished, it can lead to a press stoppage.
For this cutting, the usual flow is to first put blank paper on the pallet in the stock area according to the printing schedule and load it onto the jogger in front of the cutter. The person in charge can be seen bending over and loading one bunch at a time onto the jogger. Pallet loading after cutting is the same.
If this work continues for a long time, the load on the operator's body becomes a concern. Also, with regard to production, when manually loading paper onto the jogger or pallet, too much rubbing is a major cause of static electricity, an antagonist of printing. If the pile is strongly charged with static electricity when set on the press, production efficiency will fall.
Komori thinks the cutting process consists of the chain of jogging, cutting and pallet loading. A variety of systems, from semi-automatic to fully automatic, are available to enable the building of a flow that is gentle to both the people and the paper.
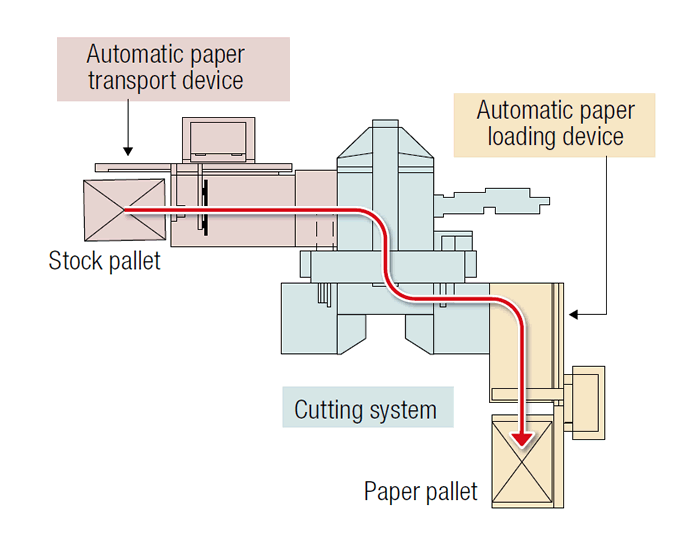
Example of automatic cutting system